The Project
Overall approach
i3upgrade aims at the intelligent and integrated upgrade of carbon sources in steel industries through hydrogen intensified synthesis processes and advanced process control technologies. The i3upgrade approach will in particular
- provide new flexible reactor concepts for the upgrade of coal-derived gases with varying composition and gas quality to methane and methanol
- optimize operation schemes by means of innovative advanced process control technologies
- enable CO2 savings through the integration of renewable hydrogen from volatile power sources
In accordance to TGC2 priority 1.3 “Innovative energy conversion cycles to increase revenue streams from coal power generation or steel industry while reducing carbon footprint “ the consortium will apply these key innovations to an integrated steel works plant.
The upgraded carbonaceous streams partly substitute fossil fuels for the energy supply as schematically drawn in Figure 1. In contrast to established synthesis processes, i3upgrade targets direct methanation and methanol synthesis of by-product gases in integrated steel works under transient conditions and with an addition of renewable hydrogen. Based on a detailed characterization of feasible operation windows, these syntheses will use advanced control strategies to address dynamic constraints of the integrated steelwork processes and of electricity grid services. Based on steel work process big-data analysis, the final proof-of-concept of the new control strategies will be done experimentally with bottled gases from the real converter and blast furnace plants as well as with a complex gas matrix from an existing coal gasifier.
Today’s processes for converting carbon oxides into value added products are designed for large scale, steady-state operation and require a certain stoichiometry of the feed gas. Since the by-product gas streams in integrated steel works do not fulfill all of these criteria, special reactors, processes and control algorithms for utilization of these by-product gases need to be developed and demonstrated. Therefore, catalytic syntheses have to be adapted in order to cope with changing gaseous educts in steelworks (i. e. blast furnace gas BFG, converter gas CG, coke oven gas COG), which are all indirectly derived from the initial feedstock coal. The proposed hydrogen intensified syntheses internally upgrade the carbonaceous streams in integrated steel industries for a final smart carbon utilization within the coal based steel making processes. Fluctuating syngas compositions and concentration of trace components in steel making processes (e. g. CG) as well as the possibility of sector coupling through electrolysis require new reactor concepts with active temperature control and high dynamics. Both proposed syntheses are going to be experimentally investigated at university laboratories and at ALFE’s industrial pre-pilot methanol unit under transient conditions with synthetic gas mixtures as well as with bottled real converter gas in case of university laboratories.
The new concepts are dedicated to the dynamic constraints of complex coal conversion plants such as intregrated steel works. In particular the integration of hydrogen from volatile sources requires the development and implementation of advanced control strategies. Online-analysis of process and market data allows for the operational optimization towards an objective function, e. g. minimization of CO2 emissions, energy consumption or production costs. i3upgrade demonstrates the feasibility of such control strategies for dynamic feed conditions of synthesis processes in bench scale test rigs with synthetic gas mixtures as well as with a complex gas matrix from an existing gasifier in a pre-pilot scale of 100 kW.
In order to increase downstream product flexibility, it is proposed to produce both methane and methanol as depicted in Figure 1 as co-products in the integrated steel works. This allows the operator to respond to changes in energy prices and to optimize energy integration, product output and the economics of the integrated steel works. Methanation and methanol synthesis are well established processes with favorable products in terms of market value, transportability and storability.
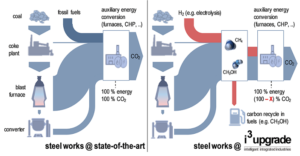
Furthermore, the products can be sold to energy and chemical process industries or internally used within the steel works (energy carrier, reducing agent). In combination with the complementary storage characteristics of the products, a beneficial sector coupling with volatile market environments (e. g. electricity, CO2 certificates) is achieved and coal based steel making as a strategic future European industry is strengthened. Therefore, in WP 6 of i3upgrade, agent-based modelling quantifies CO2 emissions and the increase of revenues for integrated steel works in the framework of new emerging volatile market behaviors with increasing renewable shares. The simulation of different market scenarios allows for the evaluation of business models when gas, electricity and emission certificate markets are going to be coupled.
Proposed methods and techniques
The main objective of the proposal i3upgrade is the integration of dynamic hydrogen intensified synthesis operated with advanced control strategies in integrated steel works in the framework of new emerging volatile markets (e. g. for electricity, CO2 emission certificates).
The “hydrogen intensified synthesis” provides a simplified process scheme for the synthesis of hydrocarbons. Any coal-derived product gas from coal gasification, coking plants, blast furnaces or converters constitutes basically of a mixture of hydrogen and CO/CO2. Due to a sub-stochiometric H2/CO ratio, synthesis of hydrocarbons from these gases dilutes the product gas generally with major amounts of CO2. Stochiometric methanation as an example requires an H2/CO ratio of 3. Lower ratios will release an excess of carbon dioxide that needs removal prior or after the synthesis. Adjusting the H2/CO ratio through addition of hydrogen makes costly CO2 removal obsolete and reduces the plant’s carbon emission in case that the hydrogen comes from renewable sources.
The proposed methods will strongly link innovative reaction concepts with control technologies based on latest machine learning algorithms and computational techniques in order to create most flexible and cost effective integrated processes.
The proposal i3upgrade includes simulation work to analyse potentials as well as the experimental proof of the proposed synthesis and control strategies and the scale-up of the synthesis units. In a first step, the potentials of hydrogen intensified synthesis in integrated steel works are evaluated in flowsheet simulations and the carbon sources in steel works are analysed in detail to create a profound data basis. This defines a parameter range which is translated to operating maps. The next step incorporates lab scale experiments with existing test rigs and synthetic gas mixtures to investigate the influence of dynamic operation on methanation and methanol synthesis. Supported by these experimental findings, the partners involved in process engineering will construct new non-adiabatic reactor concepts for methanation and methanol synthesis that fit to the conditions in dynamic synthesis (e. g. high dynamics, active temperature control). The methanation reactors are going to be integrated to existing test rigs at the scientific partners, whereas the new reactor for methanol synthesis is going to be installed at the existing pilot plant (5 – 10 m3/h) of the industrial partner ALFE. The scale-up and transient simulation of the new reactor concept gives valuable information for the industrial project partners. The operational capability of the new methanation reactor concepts is proven by the use of bottled real plant by-product gases from voestalpine (e. g. BFG, CG). The new methanol reactor will be tested under idealized conditions. Both types of synthesis reactors will be tested under user-defined transient conditions.
The second part of the project addresses the interactions of the integrated synthesis within the integrated steel works and the electricity market environment. Therefore, advanced control strategies are developed that are based on three main levels directly linked, as shown in Figure 2.
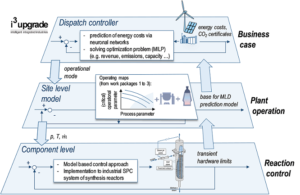
The top level consists of a dispatcher tool that allows for the optimized operation of dynamic syntheses with regard to different objectives (revenue, costs, CO2 emissions, gas quality) via application of MILP algorithms (Mixed-Integer Linear Program). Particular focus lies on the boundaries given by the industrial conditions in the VAS steel work (site level model) and to the forecast of energy market prices. These control strategies will be implemented as an advanced process control in an industrial automation system that provides set-points and gradients of relevant control parameters to the individual plant components. The controllers of methanation and methanol synthesis test rigs (component level) implement model based control approaches targeting fast transient operation and a careful consideration of catalysts operation limits (e. g. sintering temperatures). The synthesis test rigs are going to be operated with synthetic bottle mixed gases and load profiles as obtained in the voestalpine steelworks to prove their functionality. The extension of the developed synthesis and control strategies to a wider field of potential carbon sources (e. g. coke oven gas, syngas from coal gasification) and to industrial relevant scale is demonstrated in workpackage 5 by the coupled operation of a pre-pilot methanation unit with the existing 100 kW Heatpipe Reformer at EVT. Agent based modelling (WP 6) accompanies the experimental implementation in order to define the economical benefit of the dynamic integrated synthesis for steel industry in different scenarios of the emerging volatile markets. This includes OPEX optimization as well as increase of revenues through product flexibility as it is proposed in i3upgrade. The industrial partners assist in precise CAPEX estimation of the proposed techniques. The experimental data obtained in i3upgrade serves as basis for the agent based modelling (e. g. maximum possible gradients, possible gas qualities, catalyst costs).